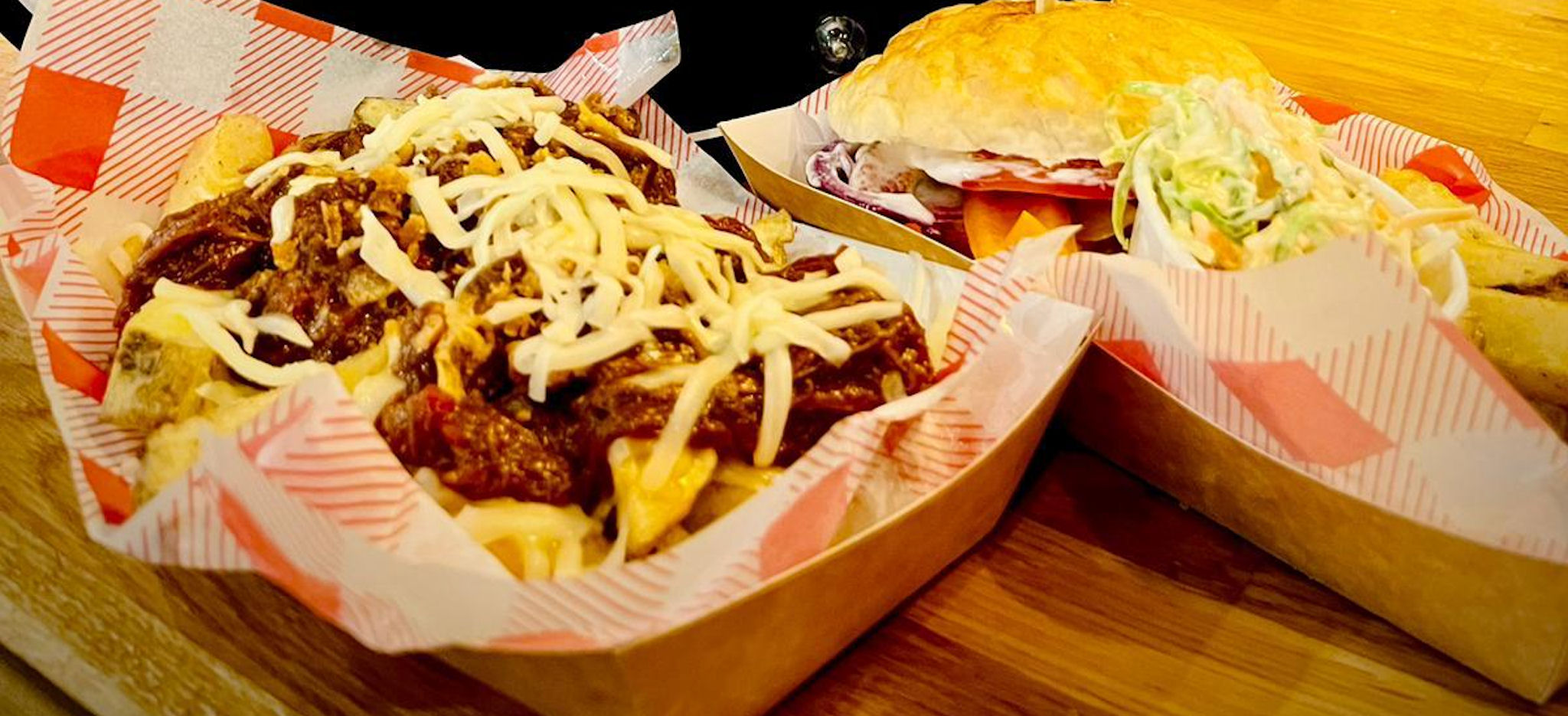
Introducing ...
Taters Gonna Tate
Chips ...
The UKs most popular side dish, 187,000 tonnes of Tater's are being sold throughout the country every year. As of late due to the demand, increase in drought for farmers, prices of the humble potato are on the rise.
Corporations are capitalising on farmers hard work and paying quoted prices per tonne on pre approved agreements of previous years, But as the supermarkets charge more per kilo to the consumer, 0 benefit is seen by the farmers and all the hard work.
Less rainfall and warmer weather contributing to a lower yield, also adding pressure to an already struggling industry trying to push the younger generation and encourage to join the farming circle.
It doesn’t sound fair does it ...
The Aim ...
Tater’s gonna Tate has a plan ... We always do
We are producing a signature product of a thick cut, skin on rustic chip. Revolutionising the way chips are delivered to small businesses & aiding with the ever cost increases of energy, products & staff.
As well as skin on fries and a few limited products of consistent high quality.
Cutting out large wholesale prices, by working directly with small, private farmers on a fair contract price & shared sale incentives means both sides of this business benefit by working in tandem.
Allowing local companies to access such a popular product at a highly competitive price, local delivery & an environmentally friendly touch, looking for sustainability & future prospects for all involved.
The Product ...
Development of the product has already wiped first 2 stages:
The benefits of this reduces necessary business costs.
The majority of chefs / humans with 2 hands have the skill set to cut a potato into chips, with TGT absorbing this costs, the labour and energy can be better focused in more vital areas of the kitchen.
Packaging ...
TGT are extremely motivated and morally obligated to push the 0 plastic ethos on site and in distribution. We work closely with leading professionals in biodegradable packaging and recyclable materials.
We are using 100% recycled cardboard, fashioned into a ‘sleeve’ style packaging, allowing the decanting process which has plagued chefs for years to be easily removed, flat packed instantly, saving 32% of unnecessary cardboard, diving costs, waste disposal & the environment. Win. Win.
The Process & Benefits ...
The reason we differ mainly from similar industry products is our blanching process, typically most large scale operations blanch in a variety of oil.
This product has negative impact to health as well as costs:
We at TGT go down a route of part Steaming, which is slightly more Labouring to us but produces a superior product , with quality , quantity & health benefits such as
We have several products available direct from suppliers:
To order & subscribe to our social media platforms is strongly advised and appreciated to ensure best offers, rolling potato puns.